The U.S. Army Corps of Engineers runs the country’s biggest hydroelectric fleet, generating 23 gigawatts of clean, renewable energy. Keeping that fleet in good operating condition and ensuring that it can provide power at competitive rates requires continual maintenance and efforts to upgrade and rehabilitate generators and dams. Currently, the Army Corps is in the middle of a major, multiyear rehabilitation effort. In this interview, Steven Miles, the director of the Army Corps’ Hydroelectric Design Center (HDC), and Daniel Rabon, its national hydropower business line manager, tell Hydro Leader about the importance of that effort and what it entails.
Hydro Leader: Please tell us about your backgrounds and how you came to be in your current positions.
Steven Miles: I am a civil engineer and licensed as a professional engineer. I have two advanced degrees: an MBA and a master’s in strategic studies. After I graduated college, I spent 27 years in the army as an engineer officer. My last job in the army was district commander of the Portland district of the Army Corps. It was in that position that I fell in love with hydropower. The Portland district has almost 7,000 megawatts (MW) of hydropower, harnessing the power of the Columbia River and its tributaries.
When I transitioned off active duty, I was a consultant for a couple years for a firm in Portland, Oregon, that had an energy business line. About 8 years ago, this army civilian job with the Army Corps became available, and I was fortunate enough to be selected. Hydropower is one of the industries that I really hoped to be able to work in after my army career. It’s a green, non-carbon-emitting, sustainable resource that brings together computer engineers, civil engineers, mechanical engineers, electrical engineers, and hydraulic engineers, to name a few.
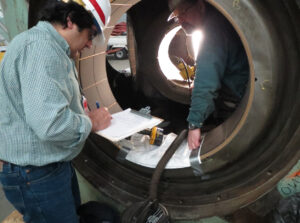
My current position is director of HDC, a national center of expertise for the engineering side of the Army Corps. HDC is predominantly based in Portland, Oregon, with other offices east of the Mississippi divide. It employs about 175 engineers and scientists, and its primary role is to serve the 16 Army Corps districts with hydropower, engineering, and analytics work. We do the major engineering of the power train for the Army Corps’ hydropower plants, and we form part of the product delivery teams of the geographic districts where those power plants are located.
Daniel Rabon: My current position is the national hydropower business line manager. I am based in our Washington, DC, headquarters. I have worked for the Army Corps for about 15 years with a bit of a break. I started in one of our district offices in Mobile, Alabama, where I was pursuing an engineering degree at the University of South Alabama. The reason I ended up with the Army Corps was that my grandmother was part of the original plant staff at the hydropower plant we have at the location where the Chattahoochee and Flint Rivers come together to form Lake Seminole in Florida.
I started out as an engineering co-op, meaning that I alternated semesters of studies with semesters of work. I ended up working at all 14 of the hydropower plants in our South Atlantic Division, so I gained a lot of hands-on experience. My last job in that region was to operate our regional engineering groups. I had about six plant engineers who worked for me across the region. After that job, I left the Army Corps and came to Washington, DC, to work for the U.S. Department of Energy (DOE) in its Waterpower Technologies Office. My current job came open in 2017, so I’ve been in this role about 3½ years.
Hydro Leader: What are your duties as the Army Corps’ hydropower business line manager?
Daniel Rabon: My section is responsible for the budget and policy of the Army Corps hydropower program. We handle the appropriated budget for 54 of our 75 hydropower projects; the rest are directly funded by the Bonneville Power Administration. We are responsible for creating, defending, and executing the budget and for all the policy that relates to the operations and maintenance of our program.
Hydro Leader: Please tell us about the Army Corps’ hydro fleet.
Daniel Rabon: The Army Corps’ hydropower fleet is the largest in the country. We have 75 hydro plants, 356 grid-connected generators, and around 23 gigawatts of installed capacity. We serve regional customers across the nation. Our power is marketed by the DOE’s Power Marketing Administrations (PMAs). Our fleet is quite old. The average age of our equipment is around 50 years. Our fleet is really important for various reasons. Historically, it played a crucial role in rural electrification. Since then, the electrical grid has changed a bit, and we’re seeing the value of using our hydropower in a lot of new ways. One of those ways is the integration of renewables, whether by participating in energy imbalance markets; by serving our customers on a more flexible; on-demand basis; or by performing ancillary services like ramping or voltage support.
Steven Miles: The average person in our country does not necessarily recognize the importance of hydropower. They may just think of hydropower facilities in the middle of rivers and think we have to get rid of them. But as Daniel pointed out, hydropower will play an important role in addressing climate change. It is a completely sustainable resource that is dependable and dispatchable, unlike solar and wind power, which are great but intermittent. Hydropower provides grid stability as well as frequency regulation. It is critical to keeping stable electricity moving. As our transmission system improves, independent system operators are able to benefit from hydropower assets outside their balancing areas to supplement MW demands and grid stability services that hydropower can provide on demand. One of hydropower’s advantages over nuclear, coal, and gas combustion generation is that it can fluctuate quickly, and flexibility is critical in the new emerging energy market. A hydropower plant can reduce or increase its output in just minutes, in contrast to a nuclear plant, the output of which is difficult to adjust once set at its base level.
Hydro Leader: How do you adjust the output of a hydro plant while it is in operation?
Steven Miles: There is a control-room operator for each of the Army Corps’ 356 generators and 75 power plants, some of whom are remote and some of whom are on site at the plant. They get signals from our partners at the DOE through the PMAs, telling them how many MW they need or what services they need for the grid. The operators can use SCADA to communicate with individual plants and to adjust the turbines and turn them on or off. A lot of that is done automatically through computers and monitored by the operators. That process is called automatic generation control (AGC).
Hydro Leader: Please tell us about the Army Corps’ ongoing rehabilitation and modernization of its hydro fleet.
Steven Miles: There are two funding streams for our fleet. One comes from the public, nonprofit power utilities in the utility associations that partner with DOE’s four PMAs. Congress has allowed these partners to fund the capital rehabilitation of our plants, which is great. A few decades ago, we had to rely on congressional appropriations. That posed problems for keeping up with the demands of the system.
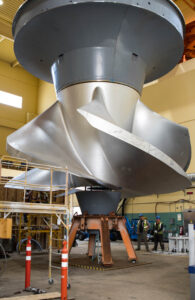
The challenge for us is that those power utilities are open to buying all sorts of generation, including natural gas, solar, and wind in addition to hydropower. They’re looking for the most inexpensive power available, so we need to keep hydropower as economically competitive as possible. Hydropower is cost challenged because of its complexity, large rotating machines, and secondary environmental mitigation costs. By contrast, a natural gas plant can be set up within short period, and natural gas is fairly cheap because of fracking and directional drilling technology.
Of our 75 power plants, 10–15 have already been modernized, and we’re working on another 20–25 right now. They’re in all different phases of rehabilitation: Some are in planning, some are in design, and some are actually being rehabilitated as we speak. Our average power plant has 5–10 generators. These are big power trains with a vertical shaft and a generator on the top, on the dry side, and a big propeller runner on the wet side that is driven by the falling water that’s coming through the dam. It takes roughly a year to completely replace a generator and put in a new turbine and generator rebuild. We replace the generators one at a time, so if a plant has five generators, four will still be running as we replace one. These projects were generally designed to be able to have at least one unit out of service at any given time. At one of our big plants, whose rehabilitation we’re designing right now, we’re considering doing two turbines at once.
There are limitations to how many turbines we can rehabilitate at once—for example, there is limited space inside the plants in which to put all the turbine parts as we disassemble them. The other limiting factor is how much power our partners can do without. At the end of the day, the PMAs still need to meet their customers’ demands.
Daniel Rabon: We tend to lag behind the industry in terms of forced outages, rates, and availability. We are trying to address that through these rehabilitations. We are also working to become more data informed. We want to make use of the data we generate to make smart decisions about additional instrumentation, to decide how to perform our day-to-day maintenance, and to consider different operational regimes as the grid continues to change. If we operate our machines differently, how is that going to change our needs for maintenance, replacement, modernization, or rehabilitation? Data can also help us predict when something is going to break and to replace it.
Hydro Leader: In addition to replacing physical components of the power plants, does rehabilitation involve software upgrades?
Steven Miles: Yes. We are now in the business of replacing digital systems with new versions. We are also working to make our turbines and power trains smart machines. That means that we are incorporating sensors and gauges for advanced diagnostics and machine condition monitoring technologies. If our operators have better diagnostics, they can save time on maintenance and avoid forced outages. Predictive and
condition-based maintenance allows us to do maintenance when it is needed, not just when an arbitrary time period has passed. We’re already seeing high payoff from these devices, including vibration sensors, pressure sensors, and temperature sensors. What we really want to avoid are forced outages, where a machine breaks or must be taken offline without warning. That puts our partners in a bind and forces them to buy power on the short-term market, which can be rather expensive.
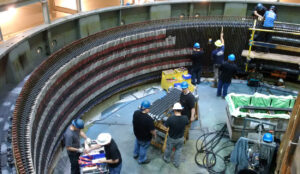
HDC staff also go to industry training events and learn about what our industry partners around the world are researching and developing. We also take part in a forum called the Center for Energy Advancement through Technological Innovation that brings hydropower owners together to share and exchange lessons they have learned. I’ll be speaking at a virtual conference in February, giving the designer’s long-term perspective on keeping hydropower generation cost competitive. The design work that HDC is doing is part of the long game—setting up our fleet to remain cost competitive years into the future.
Our main lines of effort are condition monitoring, leveraging our operational data, centralized control, and reducing the oil profile of our plants. We want to avoid the accidental release of oil from our projects. A lot of oil is involved in hydropower plants, both in the turbine hubs and in the oil cooling systems around high-bearing temperature surfaces. HDC is looking at technologies that would reduce oil use at our plants. Some of that involves new, improved designs for the propellers, which are also called turbine runners. One option is to convert some of our propellers to fixed blades. A propeller with a fixed blade doesn’t need oil inside its blades because there are no moving mechanical parts. Converting to fixed blades would reduce oil use in some cases by almost 2,000 gallons of oil per unit. The downside to the fixed-blade runner is reduced operational flexibility for ramping up and down unit generation. We’re also installing sensors and gauges on the large oil tanks in the plants to automatically warn us if there is an unintended level change.
Finally, we are working on our transformers. The transformers in a hydro plant can be as big as a two-car garage. Most of them are cooled by oil, but we are commissioning our first gas-filled transformer at Dennison Dam. It is now using SF6 insulating gas to cool its transformers. This is another way to reduce the oil profile and the risk of leaks.
Hydro Leader: How do new trends in technology, cybersecurity, and renewable energy affect the Army Corps’ modernization effort?
Daniel Rabon: We have an entity called the Hydropower Analysis Center that tries to research what kind of modernization is needed in specific places. It looks at factors like our customers’ needs, changes in the grid, the importance of flexibility in specific areas, and water availability. We work collaboratively with our PMAs and our customers to find the right solutions.
As Steve mentioned, one important factor is cost. In a lot of regions, the cost of our energy is right around the market price for natural gas–generated power. One of the ways that we are trying to reduce our prices is through centralized control. We typically sell power at the region level, and we’re seeing a big push to centralize control at the regional level, mimicking what we see a lot of other hydropower utilities do. Cybersecurity is also increasingly important. We need to keep our projects secure while we begin to shift to more centralized control.
Steven Miles: When it comes to the technology and material science that goes into these power plants, we don’t necessarily want to be on the bleeding edge of new technology, but we do want to be on the leading edge of the industry, implementing new innovative solutions. It’s critical to make sound engineering judgement, because these investments will potentially remain in service for 50–75 years.
Another area of security concern relates to the source countries where hydropower components are manufactured. It is very important that all cyber components of the hydropower system be vetted and cleared through all the appropriate country-of-origin and security screenings to ensure that they are not compromised and are cyber safe.
Hydro Leader: What is your vision for the future of the Army Corps’ hydro fleet?
Daniel Rabon: Our vision for the future of our hydropower fleet is for it to be reliable, available, dependable, and low cost. Those are lofty goals, but we’re putting a lot of effort into all of them. By working on high-quality designs and rehabilitations and becoming more data informed, we are aiming to lower costs on the operations and maintenance side and make good decisions on the capital investment side.
Steven Miles: We want to keep hydropower a reliable, competitive, and dependable resource. I feel lucky to be in the renewable energy business, particularly hydropower. Our fleet produces 23 gigawatts of clean, renewable energy— hydropower will play a critical role in decarbonizing our national grid.
Steven Miles is the director of the U.S. Army Corps of Engineers’ Hydroelectric Design Center. He can be contacted at steven.r.miles@usace.army.mil or (503) 808‑4200.
Daniel Rabon is the Army Corps’ national hydropower business line manager. He can be contacted at daniel.w.rabon@usace.army.mil or (202) 761‑4889.