John Eastwood has spent more than 50 years in the energy development industry, with experience on many continents in fields including civil and hydraulic engineering; turbine and pump manufacturing and sales; and wind, solar, and hydro project development. Mr. Eastwood’s long experience gives him insight into the development of the hydro market over the past decades, the decisive role of government regulations and subsidies, and the importance of pumped storage for the integration of renewable generation into the grid.
Hydro Leader: Would you please tell us about the phases of your long career?
John Eastwood: I joined Boving and Company Ltd. in London in 1962, after graduating from London University with a bachelor of science in civil engineering. I was a hydraulic engineer and worked in close collaboration with KMW’s hydraulic turbine laboratory in Kristinehamn, Sweden. My work focused on large hydro projects, such as Kariba Dam in present-day Zimbabwe, and reversible-pump turbines, such as those at the Cruachan and Villarino projects in Scotland and Spain, respectively. This provided the background to all my subsequent efforts in the fields of water turbines and large pumps.
In 1968, I moved from London to California, where I established Axel Johnson Engineering Corporation (AJEC) on behalf of the Swedish Axel Johnson Group, the owners of Boving and Company. My efforts were focused on the California Department of Water Resources’ California State Aqueduct, which we supplied with large spherical and butterfly valves. Building on this, AJEC subsequently supplied large valves and cooling-water pumps for nuclear power plants, including Diablo Canyon and Palo Verde. After the Three Mile Island incident, AJEC pivoted to focus on the emerging low-head hydro market in response to the enactment of the Public Utility Regulatory Policies Act of 1978. From 1982 to 1986, AJEC worked successfully to establish itself as the leading U.S. supplier of water-to-wire packages for small hydro. Of note were pioneering efforts, undertaken with Jim Besha, to supply Pit Kaplan units for ultra-low-head installations, such as Fort Miller on the Hudson River.
In 1985, I accepted the position of president of Energy Unlimited Inc., a wind development company. I left Energy Unlimited in 1986 to pursue energy development, subsequently founding and presiding over a number of businesses, including John Eastwood Associates, a hydro developer (cofounder and chairman, 1986–1993); Peak Power, a modular pumped storage developer that aimed to build distributed energy storage projects to facilitate the rapid deployment of wind and solar generation (cofounder and chairman, 1986–1991); Bering Electric Company, which supplied Soviet-built turbines and generators to the United States (cofounder and president, 1989–1992); Trinity Flywheel Power, which developed high-speed carbon-fiber flywheels for energy storage in conjunction with the Lawrence Livermore National Laboratory and subsequently became AFS Trinity (cofounder and president, 1992–2002); and finally SunLink Corporation, originally Eastwood Energy, which became a leading U.S. supplier of large, commercial-scale roof-mounting systems for solar generators (founder and executive chairman, 2002–2014). In 2017, I retired, retaining the position of advisor to the board of directors.
Hydro Leader: You did quite a lot of work on pumped storage back in the 1980s. Would you tell us about what you saw?
John Eastwood: The early 1980s was a period of dramatic progress and frenetic activity in what was called low-head hydro, though that was true of high-head hydro as well. It was stimulated, in the first instance, by the Arab oil embargo of the 1970s, which in turn stimulated regulations related to the development of private hydro projects. Around 1980– 1985, the company that I was then the president of, AJEC, became a leader in that field, providing what were called water-to-wire packages. The lesson that emerged out of that was that it was the in best interest of the United States to pursue renewables. Since there was no solar at the time and wind was in its infancy, hydro got a lot of support, including subsidies and production tax credits.
When Ronald Reagan became president, he decided that renewables, including low-head hydro and wind, were a waste of time, so in 1985, the boom became a bust over a relatively short period of time. There were many projects that had been identified in the United States that never happened because of the elimination of the necessary incentives. Fossil fuels, in particular coal and subsequently natural gas, were developed instead of low-head hydro and renewables. Now, we’re reaping the consequences in the form of global warming. The lesson is that renewable energy industries, like hydro, are the children of regulatory action. If there isn’t regulation that in some way favors or supports them, they just don’t happen.
In 1986, when I founded Peak Power, we had a concept of deploying modular pumped storage throughout the United States to serve what I felt to be the emerging need for the ability to store energy and provide peak power in conjunction with renewables. It was the right thing at the wrong time—it was simply 35 years too early!
Hydro Leader: Would you tell us about the Cruachan pumped storage project’s importance for the further development of hydro technology?
John Eastwood: Cruachan was an interesting case because prior to it, the majority of the pumped storage projects that had been developed in the world were in Europe. Such installations usually involved separate pumps and turbines, often on a common shaft. The installations were enormous in size, often with long vertical shafts topped by a motor generator. Below that would be a water turbine, and at the bottom, a multistage pump. That technology is perhaps best exemplified by the Vianden project in Luxembourg and the Ffestiniog project in northern Wales. Both construction costs and equipment costs were high. It was all driven by the fact that at that time, the pump fraternity, dominated by companies in Switzerland, weren’t comfortable with high-head single-stage machines. They preferred multistage machines.
Gradually, the idea of using single-stage machines advanced, which would reduce the overall size and cost of an installation. The use of single-stage machines required deep submergence because of cavitation considerations, but the real problem was that high-head, single-stage pump technology had not been developed by the pump industry. The pump industry, when faced with high heads, used multistage pumps, so, ironically, it was the water turbine industry that was left to develop these single-stage high-head machines. It was basically a new technology, and it enabled the development of pumped storage at a lower price than multistage installations.
Cruachan was a groundbreaker in the mid-1960s. It had a total dynamic head of 1,196 feet, which was very high for a single-stage pump. In fact, machines of that size had never been built. A similar installation with perhaps even higher head called Cabin Creek was simultaneously developed in Colorado.
There were a lot of unknowns, but everything went well after we commissioned Cruachan until we had an accident. The accident was directly attributable to the fact that there was no prior experience of large single-stage pump turbines with movable guide vanes. The guide vanes spun around and went into and destroyed the impeller—in this case, a 25‑ton stainless-steel casting. It was a bad event, but like a lot of accidents, it provided a mass of information that ended up being useful. Besides that, Cruachan has been an unqualified success and has been running continuously since we commissioned the first unit back in the late 1960s. In fact, I think there have been additions.
Today, heads on the order of 2,000 feet have been achieved, and projects with significantly higher head than that have been entertained. However, not as much has happened as might have been anticipated judging by the need, which is certainly there. That’s entirely because of the difficulty of getting permits. It’s not a technological problem or even an economic problem—it’s a regulatory problem.
Hydro Leader: In speaking about regulatory problems, are you referring primarily to the absence of incentives or the onerous process of getting the needed licenses?
John Eastwood: I’m talking about the onerous process of getting a Federal Energy Regulatory Commission (FERC) license. The FERC licensing process is slow. As a result, people are loath to consider developing hydro and pumped storage projects. The uncertainty associated with licensing affects the whole field of development and impinges on a developer’s ability to get financing.
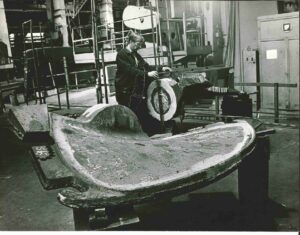
Energy policy today doesn’t really make sense. It’s driven by expediency—meaning what can be built—rather than by technological considerations or true economics. I’ve been a developer of hydro, wind, and solar projects, so I’m aware of the pitfalls. You don’t pursue something unless you believe you can get it built. Today, I would be reluctant to embark on developing a hydroelectric energy storage project. The risk is so great. You can find yourself cut off at the pass at any moment because of the perceived objections of some small group, even if they are not necessarily legitimate objections.
The regulatory factor is, in my opinion, the single biggest factor in the slow progress of hydro-based energy storage. It’s incredible that today we are obsessed with battery technology. Battery technology is fine, but its current capabilities are limited, it’s expensive, and it’s not particularly safe. It is not cost effective compared to hydro.
The idea behind Peak Power was simple: Rather than looking for a location with a water source and an elevation difference that could support a hydro project, we simply looked for a place where there was an elevation difference of around 1,000 feet. By locating a project where there was no river, we hoped to avoid the FERC licensing process, since FERC only has jurisdiction over navigable waterways. Having found a suitable location in terms of elevation difference, we would then establish whether we could bring water in, whether physically or by drilling and locating an aquifer that could charge the system. Once the system had been charged, we just had to make up for evaporation. The idea was to scatter relatively small, 25–100 megawatt installations around the grid to provide peak power, frequency regulation, power factor improvement, and other dynamic operating benefits. That would be hugely valuable today because of all the solar and wind facilities that are going in—it’s the necessary adjunct that protects a renewable energy grid from the problems of losing energy during periods when the wind doesn’t blow and the sun doesn’t shine. That vision hasn’t moved forward in the way that it should have simply because of the restrictions of the regulatory environment.
Hydro Leader: You mentioned that the Bering Electric Company transported equipment from the Soviet Union to the United States. Was that newly constructed equipment?
John Eastwood: During the Gorbachev years and after the fall of the Berlin Wall, we were idealistic about the possibilities for a rapprochement between the United States and the Soviet Union. I had the idea of starting a company, because I knew that one of the largest water turbine manufacturers was a Soviet company called Leningradsky Metallichesky Zavod (LMZ), or Leningrad Metalworks. Few people had heard of it, but because I was a hydro fan, I knew about it. My business partner at the time, Alvin Duskin, had a couple of friends who were going over to Moscow in 1988 for a conference. Coincidentally, at that conference, Gorbachev made a speech in which he welcomed people into the Soviet Union to help rebuild the economy. My friends asked me what we could do, and I suggested they go to LMZ in Leningrad (today St. Petersburg) and make a deal to buy water turbines and ship them to the United States. They asked me whether I could get to Leningrad by the following week. At the time, I was in San Francisco, so that was a bit of a daunting prospect, but we rushed over to Leningrad and formed a joint company, Bering Electric Company. It was named after the Bering Straits. The Soviets put in money, and we put in money. I ended up being the individual who had to run the company and sell Soviet-built turbines. For that reason, I contacted my friend, Jim Besha, with whom I had worked in the 1980s, and he was willing to consider Soviet turbines. We ended up providing Soviet-built turbines for some projects in New York State. I also sold a high-head Kaplan unit to the City of Takoma for the Wynoochee Project. That all ended with the 1991 coup attempt in the Soviet Union, during which Gorbachev was kept under house arrest in Crimea. Soviet credit ratings dropped to zero, and that was the end of selling turbines from the Soviet Union. We did that for about 4 years total. It was an interesting experience because nobody had been to LMZ before we had. It was, in fact, the facility that made the first nuclear weapons and Sputnik for the Soviet Union. I didn’t know this at the time, but the facility had the ability to machine propellers for submarines using five-axis machine tools acquired from Japan. As a result, we found ourselves being asked questions by entities like U.S. naval intelligence about what was going on there.
Hydro Leader: Please tell us about the changes in technology that you have seen over the course of your career in hydropower.
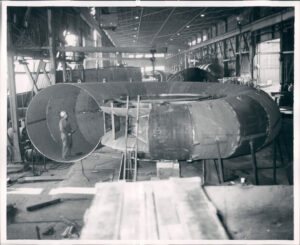
John Eastwood: I started in 1962, and I still was involved in 2017, so I have a reasonably lengthy perspective. I think the biggest change has been the shift from an analog to a digital world. When I started, everything was analog. At that time, no computers were involved in the design process, and all designs were done manually. Likewise, the turbine performance parameters were determined with laboratory test rigs, which are essentially analog computers. Today, a huge amount of work is done digitally. Computational fluid dynamics (CFD) has been translated into a numerical format so that it can be computerized. The profiling of turbine blades is done digitally and then passed to tools that can machine complex shapes. Back in the 1960s, everything was done by hand and template. The new way is much more efficient. For instance, if you were making a large water turbine impeller for a pump turbine back in the 1950s or 1960s, it would have been a single piece casting in stainless steel, it would have been hand ground, and the profiles would have been religiously copied from blown-up photographs of the model that had been used to determine the performance. Today, you make the turbine runner by welding together a bunch of components. The blades themselves are complicated, three-dimensional shapes that have often been determined by CFD and machined on a five-axis milling machine. As a result, they are precisely representative of the designed profile of the blades. These blades are then inserted into and welded to the other elements of the impeller. You end up with a much more accurate facsimile of the required shapes than used to be the case, because so much previously depended on the skills and abilities of the people who carried out the laborious hand-grinding process. It was an incredibly labor-intensive process and was also quite unhealthy because of the dust is created.
Hydro Leader: To what extent did the demand for products change over the same period?
John Eastwood: The market changed dramatically, of course. Back in the 1950s and 1960s, traditional hydro projects were still being developed in North America. That market dried up. By the 1970s and 1980s, the market in the United States and Canada had essentially evaporated. In the 1960s, for example, there were four main manufacturers of water turbines in the United States; now, there is only one. The South American market was still relatively healthy, with large projects in Brazil and Argentina, and there was still development in Africa and China. The ironic thing is that there have been a lot of big projects built in the last 20 years. The Chinese have developed big projects using low-cost labor and low-cost financing and have also successfully developed thousands of small projects. The bottom line is that hydro is an inherently limited resource because of the limited number of economically viable locations. I thought the day of large hydro had ended in the 1970s. Surprisingly, there have been some very big projects developed in the last 20 or 30 years. How long will that continue? In my opinion, it depends on the balance between environmental considerations and the need for power. Although I’m a hydro energy enthusiast, I also acknowledge that hydro isn’t always beneficial and may have negative effects on the environment.
Hydro Leader: Would you tell us about the importance of pumped storage in integrating renewables?
John Eastwood: Solar takes up a lot of space, and there is a lot of empty space in the center of the United States. To satisfy the entire energy needs of the country, you could fill a relatively small section of the United States with solar and hardly notice it. It’s an almost ideal technology, but you need energy storage to use it effectively.
The need for storage is bigger than ever before, and we have a well-established, highly efficient technology available in pumped storage that we are not deploying the way we should. In particular, it should be considered that the round-trip efficiency of a pumped storage installation can be as high as 75 percent. The round-trip efficiency, capital cost, and longevity of most battery technologies and other energy storage technologies can’t compare, even today. A hydro project can easily provide 6–10 hours of storage, which is unthinkable in the context of battery energy storage, unless capital cost is of no significance.
Hydro Leader: What are the lessons that brought you success over your years as a hydropower and energy professional?
John Eastwood: You must be courageous. Hydropower isn’t for the faint hearted. It’s risky. As I mentioned, I’ve been a developer and an equipment supplier, so I’ve seen it from both sides. When I look back on the hydro projects that I developed myself, I see significant risks. I built three projects that had tunnels, which is very risky for a private developer—those sorts of risks are almost unacceptable unless you’re slightly crazy. Risk was the biggest concern both in construction and with the equipment itself. You’re always pushing the limits of the technology. The Cruachan project, for instance, was risky. We were pumping 1,196 feet of head in a single stage. Nobody in the world had pumped to that elevation at the time, so nobody knew what was going to happen. In addition, there was the unknown cavitation risk, which increases dramatically as you increase the head. Today, you can overcome cavitation risks because you can make turbine blades more accurately, thereby minimizing potential cavitation damage. Overall, being a hydro developer requires a willingness to accept risk of a different order of magnitude than being a wind or solar developer. In the case of solar, the insolation at a project location is predictable within a band of 2 percent; with hydro, the hydrological risk can be as high as 100 percent.
John Eastwood is a longtime energy professional who was most recently the founder of the SunLink Corporation. He can be contacted at jeastwood@sprintmail.com or (415) 990‑3176.